HELLER solutions at Knödler-Getriebe
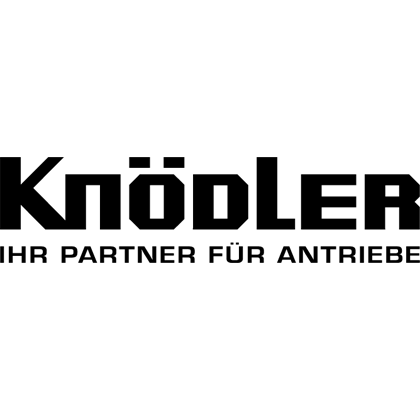
The strength of the HELLER H 14000 power pack is in the detail
Gear units with torques of up to 400,000 Nm and outputs up to 1,000 kW are the calling card of Knödler-Getriebe GmbH. The primary aim of investing in the HELLER H 14000 4-axis machining centre was to create reserves in a universal and reliable manner.
Task
- to produce gear housings with torques of 500 to 400,000 Nm and unit weights of up to 12 t
- high daily load with very high chip removal rates and incredible cutting performance
- long service life and highest possible machine precision
- universal flexibility with adequate reserves to meet one-off customer requests
Project scope & solution
- H 14000 4-axis machining centre with 4-speed gear unit/machining unit: 6,000 rpm, 2,292 Nm, 60 kW
Result
- The performance, the mechanical structure and the structural analysis support sustained use of the machine.
- The H 14000 paved the way to pre-milling bearing seats with diameters of up to 600 mm with an insert miller in one cut and then finish-milling with a special solid carbine end milling cutter in a circular fashion. This puts roundness of 5 μm and outstanding Rz surface qualities in the range of 6 to 8 μm on the test records.
- The H 14000 also offers reserves for applications such as the milling of spiral conveyors that involves the use of a severely protruding special tool of 600 mm in length.
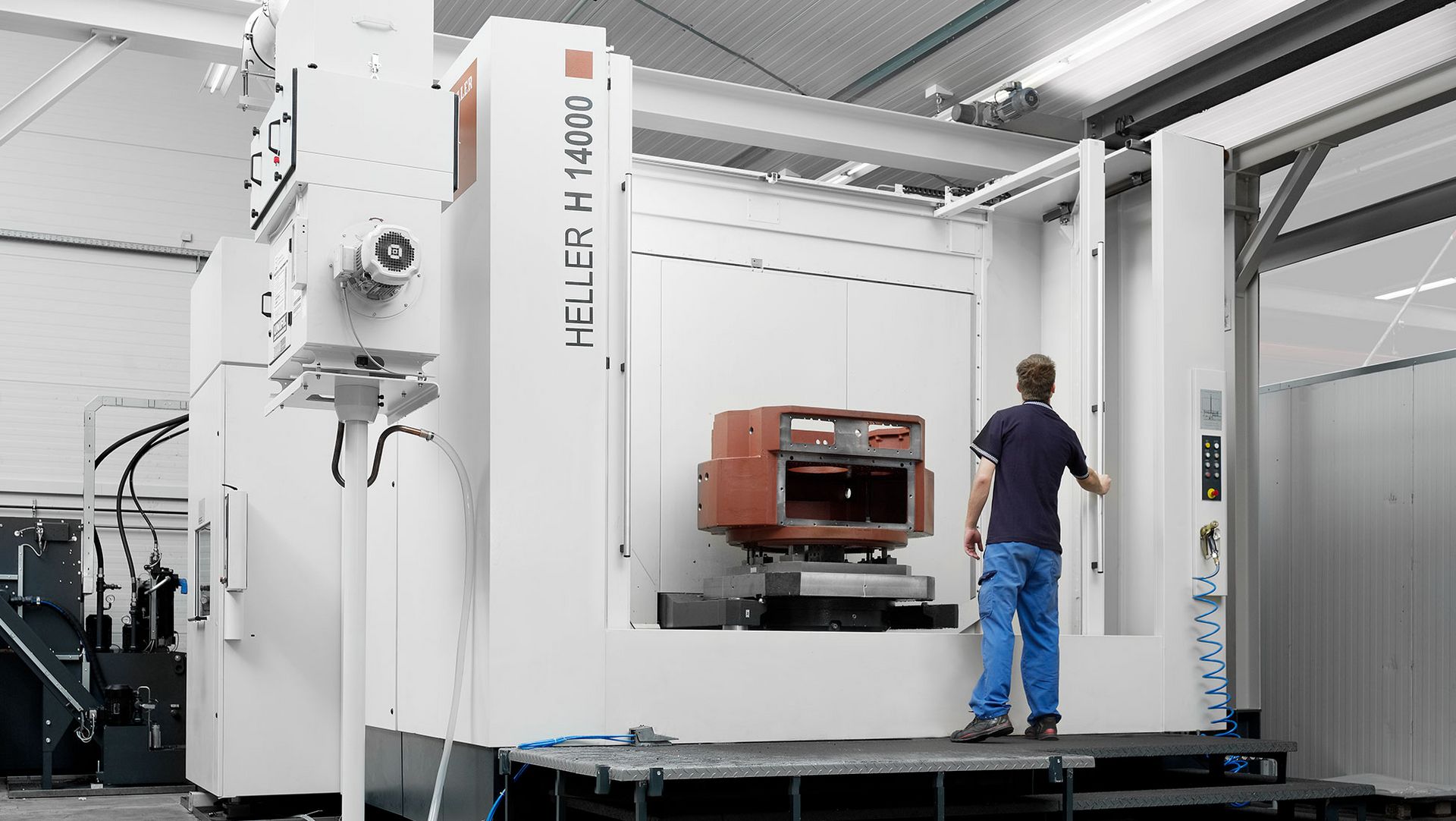
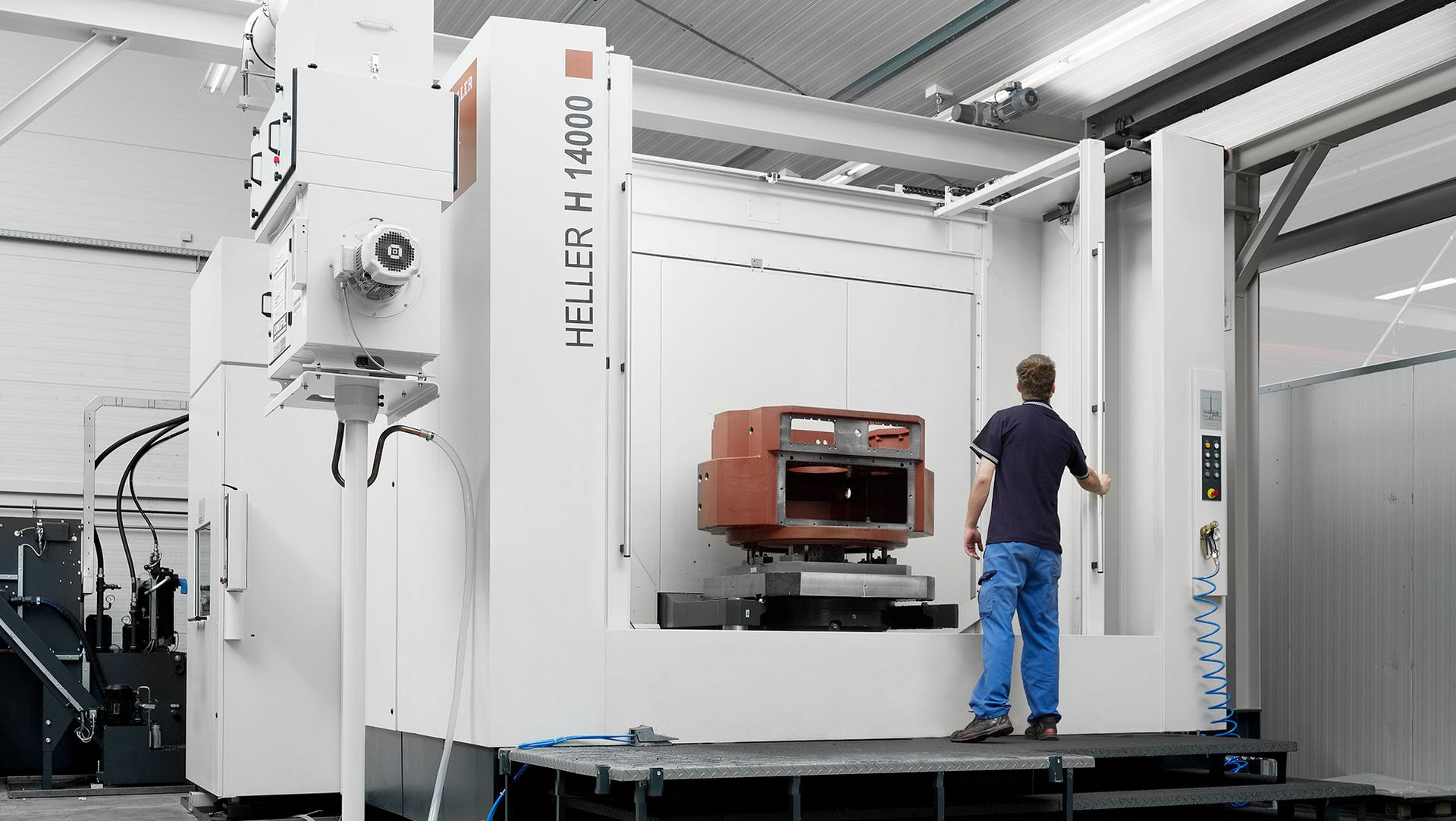
Contact
Contact
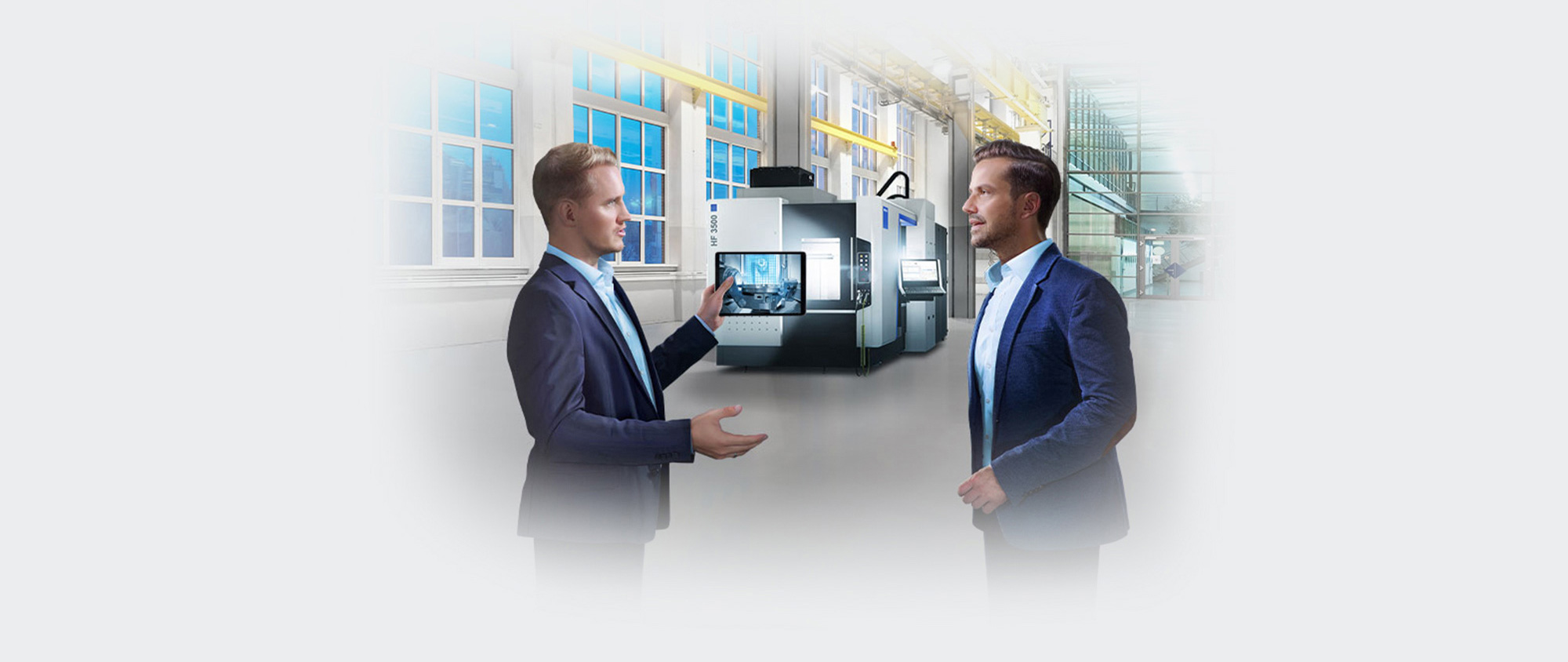
Sales & Services
Do you have questions about our products and services? Please get in touch with us, we are here for you! Benefit from our global HELLER network with knowledgeable sales and service contacts located in your region.
Find your nearest personal contact.
No results could be found.
You might also be interested in
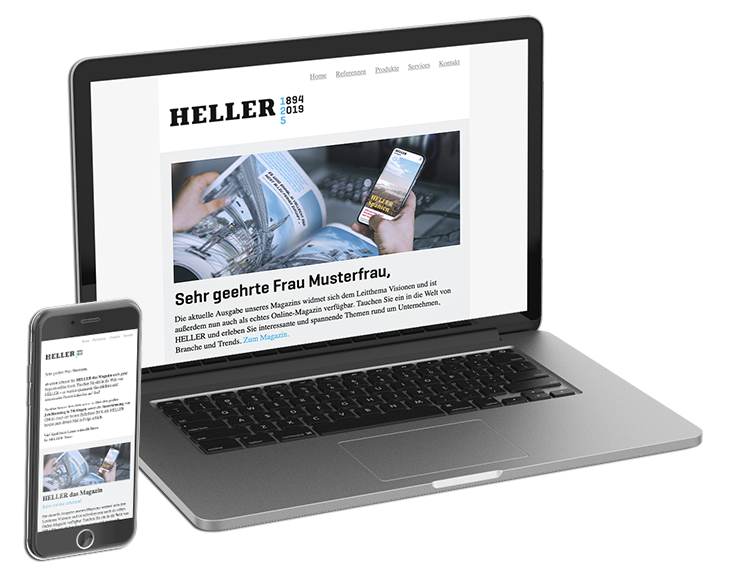
HELLER Newsletter
Register now!
The HELLER Newsletter provides you with information about all current topics concerning our company, our products and services as well as upcoming trade shows and events. Register now to make sure you never miss any news from the HELLER Group!