HELLER automation solutions
Open to standards – flexible for individual solutions
The main purpose of automated manufacturing and production centres is to achieve a reduction in idle times, thus optimising system availability. However, the requirements of the individual industries vary greatly, resulting in a wide range of different solutions available in the market. Meanwhile, a number of specialists have become well established in the market who co-operate with HELLER as part of a best-in-class partnership. In addition, HELLER offers proprietary automation solutions that will ideally combine with the highly productive HELLER machining centres.
Automation solutions by and with HELLER always comprise customised concepts that we specifically develop to suit your production. We analyse your requirements and design a solution to provide you maximum added value. For this purpose, we draw on standardised solutions as far as possible. Technical options range from simple pallet changers or linear/rotary pallet storages to flexible loading robots right up to the combination with a rack system, also for tool storage.
Pallet automation

Pallet changer
First automation level, integrated into the machine. Perfect for serial production with medium and large lot sizes.
- reliable, automatic pallet change with hydraulic lifting/swivelling drive
- fast transportation between work area and workpiece setting station
- setting of fixtures during workpiece machining
- loading during machining by the operator or a robot
- basis for further automation levels such as workpiece loading with robot or pallet automation
- short pallet change time for highest productivity
- compact system thanks to full integration in the machine
- excellent safety, also when handling heavy payloads thanks to clamping system with fail-safe pallet clamping
- ergonomic design with low loading sill for optimum access to fixture and workpiece
Options:
- automatically rotated pallet
- automatically actuated doors at workpiece setting station
- pallet location check
- media interface for hydraulic workpiece clamping
- pneumatic unclamp/position control adjustable at main operating unit (IO link)

Linear storage
Automatic handling of pallets for optimised flexibility. Perfect for serial production with medium and large lot sizes.
- automatic setting of pallets including fixture and workpiece
- storing of machine pallets on up to 15 storage places per container depending on type and size
- automatic pallet transportation between storage location, setting station and machine
- organisation of production jobs including administration and prioritisation
- control and monitoring of the production process by means of control technology
- efficient production with a large parts mix and small batch sizes
- loading of prepared pallets and fixtures from the container directly into the machine
- maximum flexibility with changing production jobs (e.g. NC program or tool management)
- optimal capacity utilisation with continuous pallet feed to one or multiple machines
- high storage capacity with low investment per storage place
- standardised complete solutions for fast installation and commissioning
Options:
- extension container
- additional loading station(s)
- various software packages and options
- media interface for hydraulic workpiece clamping

Rotary storage
Automatic handling of pallets for optimised flexibility with low space requirement. Perfect for serial production with medium and large lot sizes.
- automatic setting of pallets including fixture and workpiece
- storage of machine pallets on up to 13 storage places depending on type and size
- automatic pallet transportation between storage location, setting station and machine
- organisation of production jobs including administration and prioritisation
- control and monitoring of the production process by means of control technology
- efficient production with high component variance
- maximum flexibility with changing production jobs (e.g. NC program or tool management)
- low space requirement thanks to compact design
- loading of set-up pallets and fixtures from the storage directly into the machine
- optimal capacity utilisation with continuous pallet feed to one or two machines
Options:
- extension: max. 7 additional storage places
- interface for integration of a second machine
- second loading station
- media interface for hydraulic workpiece clamping
- various software packages and options
- automatically rotating setup station
Workpiece automation

Robot
Automatic loading and unloading of workpieces, fixtures and pallets as well as automation of additional handling jobs. Perfect for serial production with medium and large lot sizes.
- workpiece handling with high process reliability of all parts from raw to finished
- automatic loading of single and multiple setups in all machine types
- automatic setting of pallets and fixtures as customer-specific solutions
- linking of individual process steps and work stations inside the robot cell
- implementation of further tasks such as deburring, brushing, cleaning, testing
- automated 24/7 production with low component variance
- customer-specific automation of one or several machines with a stationary or moving robot
- small-footprint solution for optimum floor utilisation
- high process reliability thanks to repeatability and optimum robot availability
- optimum utilisation of machine capacity with continuous material supply and minimisation of spindle downtimes
- safe interaction thanks to defined interactions between operator and robot
Machine options:
- standardised machine interface for robot loading onto the setting station
- media interface for hydraulic workpiece clamping
- location and unclamping check adjustable at main operating unit (IO link)

Linear gantry loader
Linking of plant components in production lines with maximum output. Perfect for serial production with short durations and highest production volume.
- workpiece transportation between the plant components from raw to finished, with or without workpiece carrier
- loading of the HELLER machining centres from top into the work area and automatic unloading after machining
- loading of further plant components like measuring, washing, assembly, leak test, storage systems etc.
- connection of individual linear gantries by ground-based conveying systems, such as conveyor belts and automated guided vehicles
- control technology responsible for manufacturing process control and monitoring
- optimal workpiece flow through project-specific configuration of linear axes (number and length)
- agile automation system
- fast workpiece exchange at the machining centres and system components
- best possible utilization of space thanks to workpiece top transfer
- optimum accessibility to all areas of the machine thanks to loading from above
- minimal chip and coolant carryover
Tool automation

Background tool magazine
Central tool provision for several machines. Perfect for production systems with maximum of flexibility and automation.
- automatic tooling of tools directly in the tool magazine by means of gantry loader
- automatic tool transportation between background magazine and machine, as well as between the machines
- central storage of tool set (number of tools according to customer requirement)
- central tool management with current state of all tools in the tool magazine of the machines and in the background magazine
- job-related investigation of the tool requirement under consideration of the tool state, the remaining tool life and the usage time as well as advance planning
- integration into the higher-level control technology of the workpiece automation system for optimum order processing
- maximum flexibility for changing production tasks
- central storage of tools for all machines in the network
- central tooling station for all machines in the network
- reduced tool inventory due to order-related use of tools in different machines
- optimum planning thanks to up-to-date information on the condition and availability of tools
- automatic tool logistics and central tool provision
- smaller tool magazines possible at the individual machines
Contact
Contact
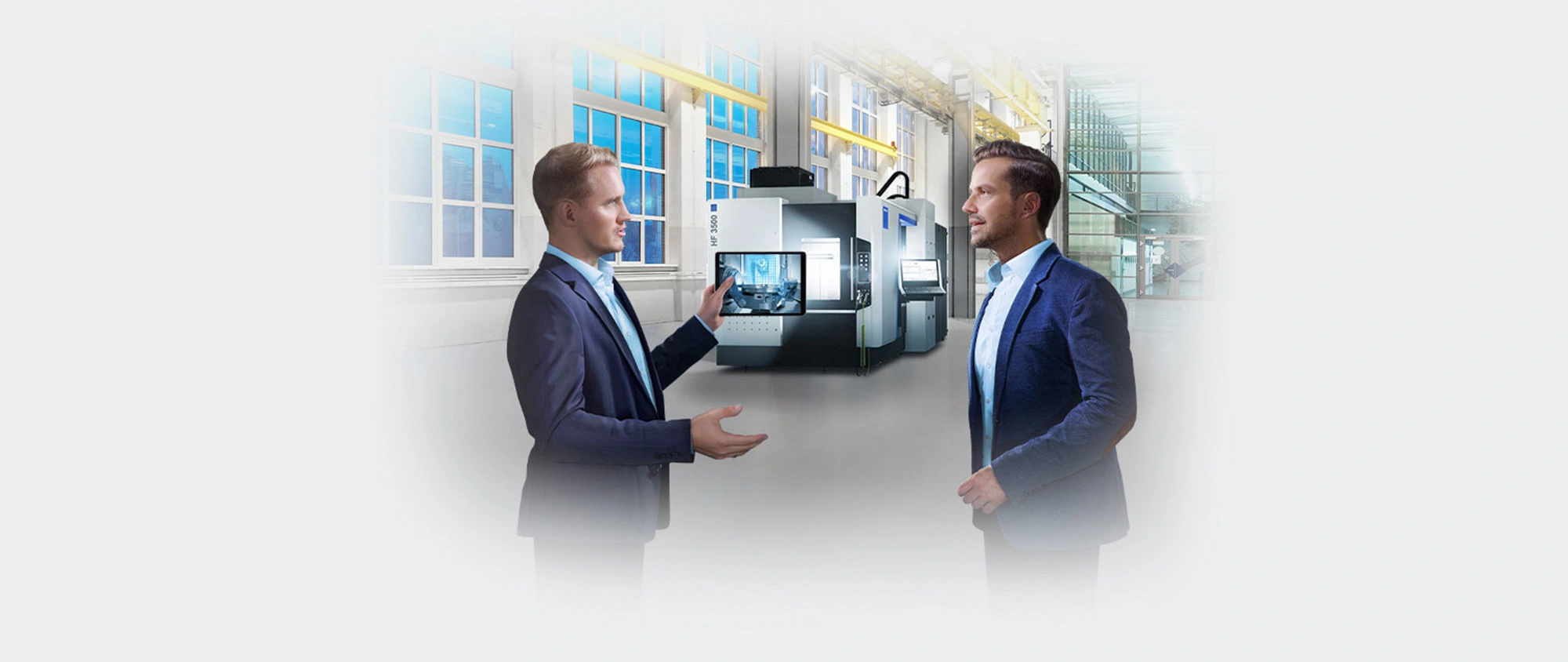
Sales & Services
Do you have questions about our products and services? Please get in touch with us, we are here for you! Benefit from our global HELLER network with knowledgeable sales and service contacts located in your region.
Find your nearest personal contact.
No results could be found.
You might also be interested in
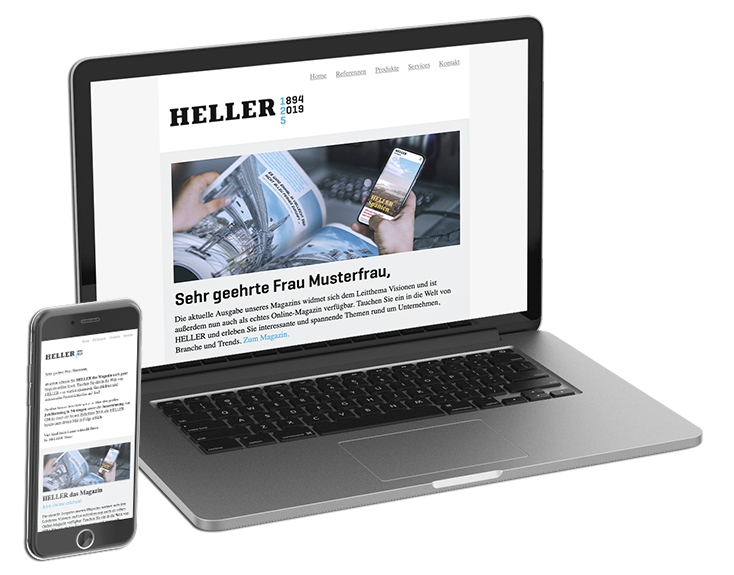
HELLER Newsletter
Register now!
The HELLER Newsletter provides you with information about all current topics concerning our company, our products and services as well as upcoming trade shows and events. Register now to make sure you never miss any news from the HELLER Group!